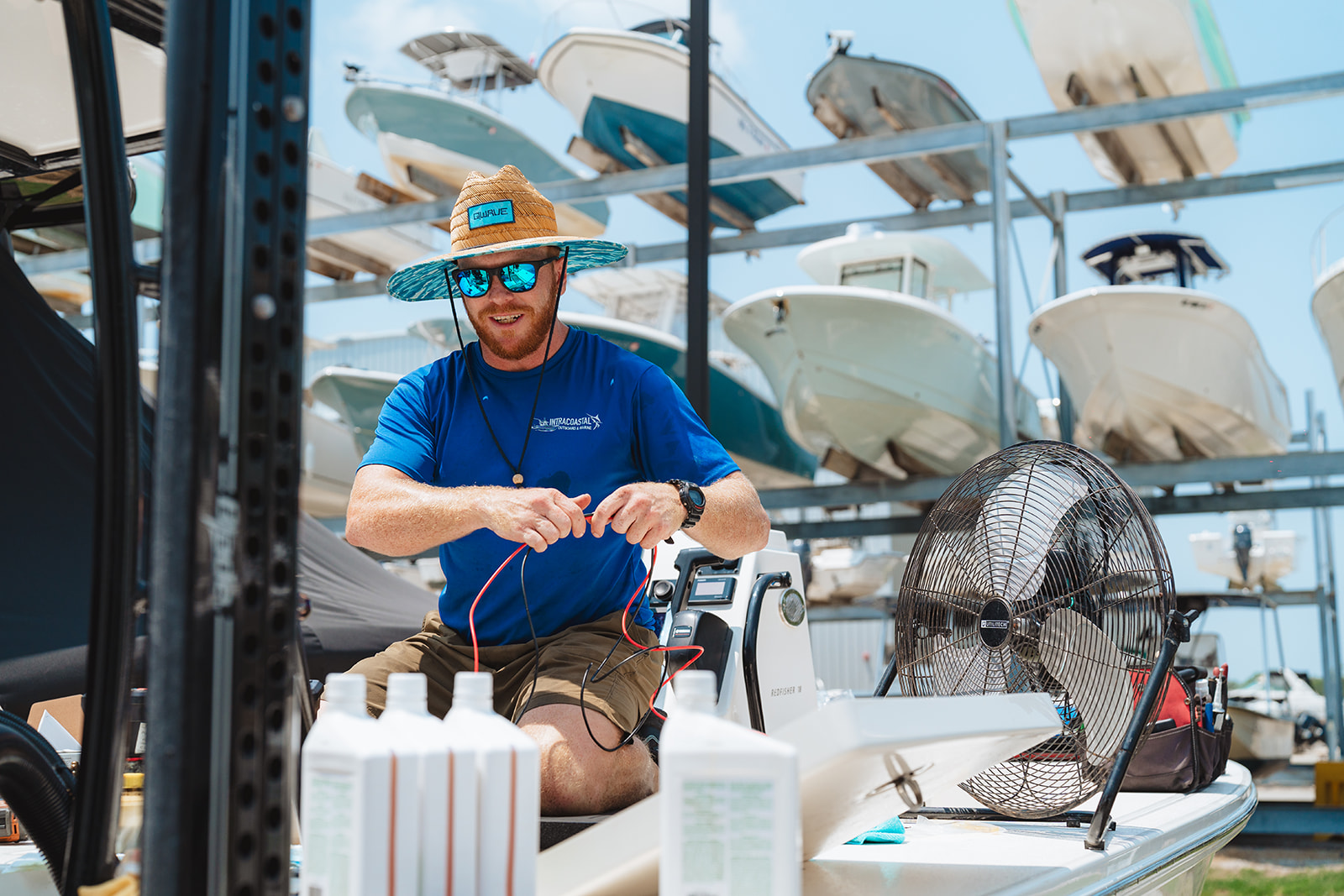
As we step into 2024, businesses across the globe are grappling with the increasing costs of maintenance, repairs, and operations. Inflation, labour shortages, and rising material costs are placing unprecedented pressure on property managers and marina operators to do more with less. In this challenging environment, optimizing your maintenance budget is not just a financial necessity—it’s a strategic imperative.
The good news? With the right approach and tools, you can significantly reduce costs while maintaining or even improving the quality of your maintenance operations. Here’s how to optimize your maintenance budget in 2024.
1. Embrace Preventive Maintenance to Avoid Costly Repairs
Preventive maintenance is one of the most effective ways to manage costs. Instead of waiting for equipment to fail, which can lead to expensive emergency repairs, a preventive approach ensures that issues are identified and addressed before they escalate.
Key Steps:
- Schedule Regular Inspections: Implement a routine inspection schedule to catch potential issues early. This proactive approach helps prevent unexpected breakdowns that can be costly.
- Use Predictive Analytics: Leverage modern maintenance management systems like esyndico, which can use data analytics to predict when equipment is likely to fail, allowing for timely maintenance before a breakdown occurs.
Outcome:
By focusing on preventive maintenance, you can reduce the frequency and severity of repairs, thereby lowering overall maintenance costs.
2. Streamline Processes with Digital Tools
Manual processes and paper-based systems are not only inefficient but also prone to errors that can lead to higher costs. Digital tools and platforms can help you streamline your maintenance operations, ensuring that every dollar is spent wisely.
Key Steps:
- Automate Workflows: Utilize maintenance management software like esyndico to automate routine tasks such as scheduling, parts ordering, and job assignment. This reduces administrative overhead and frees up your team to focus on higher-value activities.
- Centralize Data: Use a single platform to manage all maintenance activities. Centralizing data allows for better decision-making and reduces the risk of costly errors due to miscommunication or data silos.
Outcome:
Streamlining processes with digital tools not only saves time but also reduces costs associated with errors and inefficiencies.
3. Optimize Your Inventory Management
Holding too much inventory ties up capital that could be used elsewhere, while holding too little can lead to expensive rush orders and downtime. Effective inventory management is key to balancing these two extremes.
Key Steps:
- Track Inventory Levels: Use digital tools to monitor your inventory in real-time, ensuring you always have the right parts on hand without overstocking.
- Implement Just-in-Time Ordering: Work with suppliers to implement a just-in-time inventory system, where parts and materials are ordered as needed, reducing the costs associated with holding excess inventory.
Outcome:
Optimized inventory management reduces storage costs and minimizes the financial impact of holding excess inventory, while also ensuring that you have the necessary parts to avoid downtime.
4. Train and Empower Your Team
An often overlooked aspect of maintenance budget optimization is the skills and efficiency of your maintenance team. Well-trained employees who understand the latest tools and techniques can work more efficiently, reducing labor costs and improving the quality of work.
Key Steps:
- Invest in Training: Regularly train your team on the latest maintenance practices, tools, and safety protocols. A knowledgeable team can prevent costly mistakes and perform more efficiently.
- Empower with Tools: Equip your team with the tools they need to do their job effectively. This includes mobile access to maintenance software, enabling them to log issues, track work orders, and update inventory on the go.
Outcome:
A well-trained and equipped team can perform maintenance tasks more efficiently, reducing both labor costs and the likelihood of errors.
5. Monitor and Analyze Maintenance Costs Regularly
To effectively manage your maintenance budget, it’s crucial to regularly monitor and analyze where your money is going. This allows you to identify areas where you can cut costs without compromising on quality.
Key Steps:
- Track Expenses: Use your maintenance management software to track all maintenance-related expenses in real-time. This includes labor, materials, equipment, and contractor costs.
- Analyze Data: Regularly analyze your maintenance data to identify trends, inefficiencies, and opportunities for cost savings. For example, you might find that certain equipment consistently incurs higher repair costs, indicating that it may be time for replacement or a different maintenance approach.
Outcome:
By continuously monitoring and analyzing your maintenance costs, you can make informed decisions that optimize your budget and improve the efficiency of your operations.
6. Consider Outsourcing Non-Core Maintenance Tasks
Outsourcing non-core maintenance tasks can be a cost-effective way to manage your budget. This allows your internal team to focus on more strategic tasks while specialized contractors handle routine or complex repairs.
Key Steps:
- Evaluate Outsourcing Opportunities: Identify maintenance tasks that are time-consuming or require specialized skills that are not available in-house. Consider outsourcing these tasks to reliable contractors.
- Negotiate Contracts: Work with contractors to negotiate favorable terms that include clear service level agreements (SLAs) and cost controls.